Porosity in Welding: Identifying Common Issues and Implementing Finest Practices for Prevention
Porosity in welding is a pervasive issue that typically goes unnoticed until it causes significant issues with the honesty of welds. This common defect can compromise the stamina and longevity of welded structures, posturing safety threats and causing expensive rework. By understanding the source of porosity and applying effective avoidance strategies, welders can considerably enhance the top quality and reliability of their welds. In this conversation, we will explore the crucial factors adding to porosity formation, examine its damaging results on weld efficiency, and go over the most effective techniques that can be adopted to decrease porosity incident in welding procedures.
Typical Reasons For Porosity

Making use of filthy or wet filler products can present contaminations right into the weld, adding to porosity issues. To minimize these typical reasons of porosity, thorough cleaning of base steels, correct securing gas selection, and adherence to ideal welding specifications are important techniques in attaining top quality, porosity-free welds.
Effect of Porosity on Weld Quality

The visibility of porosity in welding can considerably compromise the architectural honesty and mechanical properties of bonded joints. Porosity develops spaces within the weld metal, damaging its overall toughness and load-bearing ability. These spaces function as stress and anxiety concentration points, making the weld much more vulnerable to splitting and failing under used lots. In addition, porosity can minimize the weld's resistance to rust and other ecological elements, even more decreasing its durability and performance.
Welds with high porosity levels tend to display reduced influence strength and decreased capacity to flaw plastically before fracturing. Porosity can hinder the weld's capability to effectively send forces, leading to early weld failure and possible safety threats in critical structures.
Best Practices for Porosity Avoidance
To boost the structural integrity click over here now and high quality of bonded joints, what specific steps can be executed to lessen the incident of porosity throughout the welding procedure? Porosity avoidance in welding is essential to make certain the honesty and toughness of the last weld. One reliable technique is proper cleansing of the base steel, removing any type of impurities such as rust, oil, paint, or wetness that can lead to gas entrapment. Guaranteeing that the welding devices is in good condition, with clean consumables and suitable gas circulation prices, can also considerably lower porosity. Additionally, maintaining a steady arc and regulating the welding criteria, such as voltage, current, and take a trip rate, assists create a regular weld swimming pool that lessens the risk of gas entrapment. Using the proper welding method for the particular material being bonded, such as changing the welding angle and gun position, can even more protect against porosity. Regular assessment of welds and prompt remediation of any concerns determined throughout the welding procedure are essential practices to stop porosity and create top quality welds.
Importance of Proper Welding Methods
Implementing proper welding techniques is vital in ensuring the structural integrity and quality of welded joints, building upon the structure of efficient porosity avoidance steps. Too much warmth can lead to enhanced porosity due to the entrapment of gases in the weld swimming pool. In addition, using the proper welding criteria, such as voltage, current, and travel speed, is crucial for accomplishing audio welds with marginal porosity.
Additionally, the selection of welding process, whether it be MIG, TIG, or stick welding, must align with the certain needs of the project to make certain optimum outcomes. Appropriate cleaning and preparation of the base steel, in addition to selecting the appropriate filler product, are likewise important parts of efficient welding methods. By sticking to these ideal techniques, welders can minimize the danger of porosity development and generate top quality, his explanation structurally sound welds.
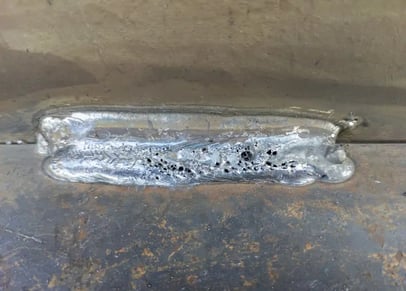
Evaluating and Quality Assurance Measures
Quality control actions play an essential function in confirming the honesty and reliability of welded joints. Checking treatments are necessary to discover and stop porosity in welding, making certain the toughness and durability of the end product. Non-destructive testing methods such as ultrasonic screening, radiographic screening, and aesthetic examination are typically used to determine possible problems like porosity. These strategies enable the analysis of weld top quality without endangering the honesty of the joint. What is Porosity.
Post-weld assessments, on the various other hand, evaluate the last weld for any defects, consisting of porosity, and validate that it satisfies specified standards. Implementing a thorough top quality control strategy that includes detailed screening treatments and examinations is critical to reducing porosity concerns and ensuring the overall high quality of bonded joints.
Conclusion
To conclude, porosity in welding can be a common problem that affects the top quality of welds. By recognizing the common causes of porosity and executing finest practices for avoidance, such as appropriate welding strategies and screening actions, welders can ensure premium quality and reputable welds. It is vital to prioritize prevention techniques to lessen the incident of porosity and preserve the use this link stability of bonded structures.